Industrial Acoustic Sound Enclosures FanAir Company designs and
Por um escritor misterioso
Descrição
FanAir Co. 10 Ft x 10Ft x 12 FT Fiberglass Acoustic Sound Enclosure Installed at Anacortes, Washington Waste Water Treatment Plant. FanAir Co. 6 Ft x 6 Ft x 5 FT Fiberglass Acoustic Sound Enclosure designed and built for a Fiberglass Odor Control Blower for a Biofilter Located in Orange, County, Ca. FanAir Company Ph (714) | Fx (714) Industrial Acoustic Sound Enclosures Installation examples:
Sound enclosures shall be as manufactured only by companies with a minimum of 5 years manufacturing experience of noise control equipment for fans, blowers, pumps and or compressors. Sound enclosure manufacturer shall guarantee a minimum of -15 dB A at 3 Feet insertion loss from noise producing equipment to be enclosed. Sound enclosure manufacturer shall obtain from the blower equipment manufacturer listed on schedule, the sound level ratings based on AMCA test standard 300, the housing radiated noise level and the inlet and discharge noise level ratings. Sound enclosure manufacturer shall coordinate with the equipment manufacturer listed on schedule requirements for cooling, temperature rise and special provisions for Inlet ducting, discharge ducting, appurtenances such as dampers, Flexible duct connections, inlet or discharge silencers, intake filters, vibration isolators, seismic restraints, motors, drives and guards, electrical connections, electrical safety disconnect switches. The sound enclosure manufacturer shall also make special provisions to allow access to serviceable items such as bearings, lubrication, seals, dampers, belts, motors and access doors. Sound enclosure manufacturer will provide and place a 10 x 14 warning sign, on each access door, indicating equipment is to be shut down and locked out prior to entry. PRODUCT 2.0 The sound enclosure shall be a rigid complete enclosure using Fiberglass Reinforced Plastic and shall be lined with acoustical materials as listed below. Sound adsorbing materials shall be a minimum of 1/2 thick,.5 Lb/Sq.Ft. loaded vinyl barrier acoustic insulating foam, with a vinyl facing. Acoustic Insulation shall have a NRC rating of.48 and an STC rating of 31. Acoustic lining shall be capable of being steam cleaned and shall be chemical resistant. Exterior fiberglass structure shall have a Class I E 84 flame spread rating of 25 or less. a The sound enclosure shall be vertically split in such a manner to allow one half of the enclosure of the enclosure to be removed without disturbing the intake or discharge duct connections. The 2 sections of the enclosure shall be joined by use of quick release latches. The sound enclosure shall be provided with a minimum of 2 Each, PVC extended grease lubrication lines extended to the outside wall of the enclosure terminating to Zerk relief fittings to facilitate lubrication of the bearings and shaft seal. The Zerk fittings shall be marked with the proper grade of grease and the items lubricated. The sound enclosure shall be provided with factory pre-cut penetrations to facilitate intake and discharge ductwork or pipe. The precut penetrations shall be 2 Inches overall larger than the duct or pipe diameter. Additional filler strips shall be provided with insulation to close within ¼ of the ductwork. The sound enclosures shall be provided with 1 Each, spun aluminum AMCA Type B, roof mounted exhaust fan furnished with roof curb. The exhaust fan shall be selected to provide no less than 30 air changes per hour or 1 air change every 2 minutes. The exhaust fan shall have a V, ( TENV or Explosion Proof Motor ) and be factory pre-wired to an external junction box. All electrical connections shall be UL rated for Class I, Division I, Group D. Sound enclosure shall be fitted with an acoustical intake louver, located at low point of side wall of enclosure, furthest point away from exhaust fan. Louver shall be provided with insect screen and be sized for a minimum transmission noise loss and pressure drop. Sound enclosure shall be provided with one or more of the following: 24 x 24 bolted or hinged inspection door, inspection window, constructed in Lexan or similar material, locking hinged access door minimum of 24 H x 30 Wide. Sound enclosure manufacturer shall provide certified drawings, sound test data showing transmission loss, Installation, operation and maintenance instructions and a 2 year warranty. Sound enclosure manufacturer shall demonstrate a minimum of 10 previous instances of sound enclosure installations with industry references. Sound Enclosures shall be as manufactured by FanAir Company, Orange, California..
Sound enclosures shall be as manufactured only by companies with a minimum of 5 years manufacturing experience of noise control equipment for fans, blowers, pumps and or compressors. Sound enclosure manufacturer shall guarantee a minimum of -15 dB A at 3 Feet insertion loss from noise producing equipment to be enclosed. Sound enclosure manufacturer shall obtain from the blower equipment manufacturer listed on schedule, the sound level ratings based on AMCA test standard 300, the housing radiated noise level and the inlet and discharge noise level ratings. Sound enclosure manufacturer shall coordinate with the equipment manufacturer listed on schedule requirements for cooling, temperature rise and special provisions for Inlet ducting, discharge ducting, appurtenances such as dampers, Flexible duct connections, inlet or discharge silencers, intake filters, vibration isolators, seismic restraints, motors, drives and guards, electrical connections, electrical safety disconnect switches. The sound enclosure manufacturer shall also make special provisions to allow access to serviceable items such as bearings, lubrication, seals, dampers, belts, motors and access doors. Sound enclosure manufacturer will provide and place a 10 x 14 warning sign, on each access door, indicating equipment is to be shut down and locked out prior to entry. PRODUCT 2.0 The sound enclosure shall be a rigid complete enclosure using Fiberglass Reinforced Plastic and shall be lined with acoustical materials as listed below. Sound adsorbing materials shall be a minimum of 1/2 thick,.5 Lb/Sq.Ft. loaded vinyl barrier acoustic insulating foam, with a vinyl facing. Acoustic Insulation shall have a NRC rating of.48 and an STC rating of 31. Acoustic lining shall be capable of being steam cleaned and shall be chemical resistant. Exterior fiberglass structure shall have a Class I E 84 flame spread rating of 25 or less. a The sound enclosure shall be vertically split in such a manner to allow one half of the enclosure of the enclosure to be removed without disturbing the intake or discharge duct connections. The 2 sections of the enclosure shall be joined by use of quick release latches. The sound enclosure shall be provided with a minimum of 2 Each, PVC extended grease lubrication lines extended to the outside wall of the enclosure terminating to Zerk relief fittings to facilitate lubrication of the bearings and shaft seal. The Zerk fittings shall be marked with the proper grade of grease and the items lubricated. The sound enclosure shall be provided with factory pre-cut penetrations to facilitate intake and discharge ductwork or pipe. The precut penetrations shall be 2 Inches overall larger than the duct or pipe diameter. Additional filler strips shall be provided with insulation to close within ¼ of the ductwork. The sound enclosures shall be provided with 1 Each, spun aluminum AMCA Type B, roof mounted exhaust fan furnished with roof curb. The exhaust fan shall be selected to provide no less than 30 air changes per hour or 1 air change every 2 minutes. The exhaust fan shall have a V, ( TENV or Explosion Proof Motor ) and be factory pre-wired to an external junction box. All electrical connections shall be UL rated for Class I, Division I, Group D. Sound enclosure shall be fitted with an acoustical intake louver, located at low point of side wall of enclosure, furthest point away from exhaust fan. Louver shall be provided with insect screen and be sized for a minimum transmission noise loss and pressure drop. Sound enclosure shall be provided with one or more of the following: 24 x 24 bolted or hinged inspection door, inspection window, constructed in Lexan or similar material, locking hinged access door minimum of 24 H x 30 Wide. Sound enclosure manufacturer shall provide certified drawings, sound test data showing transmission loss, Installation, operation and maintenance instructions and a 2 year warranty. Sound enclosure manufacturer shall demonstrate a minimum of 10 previous instances of sound enclosure installations with industry references. Sound Enclosures shall be as manufactured by FanAir Company, Orange, California..
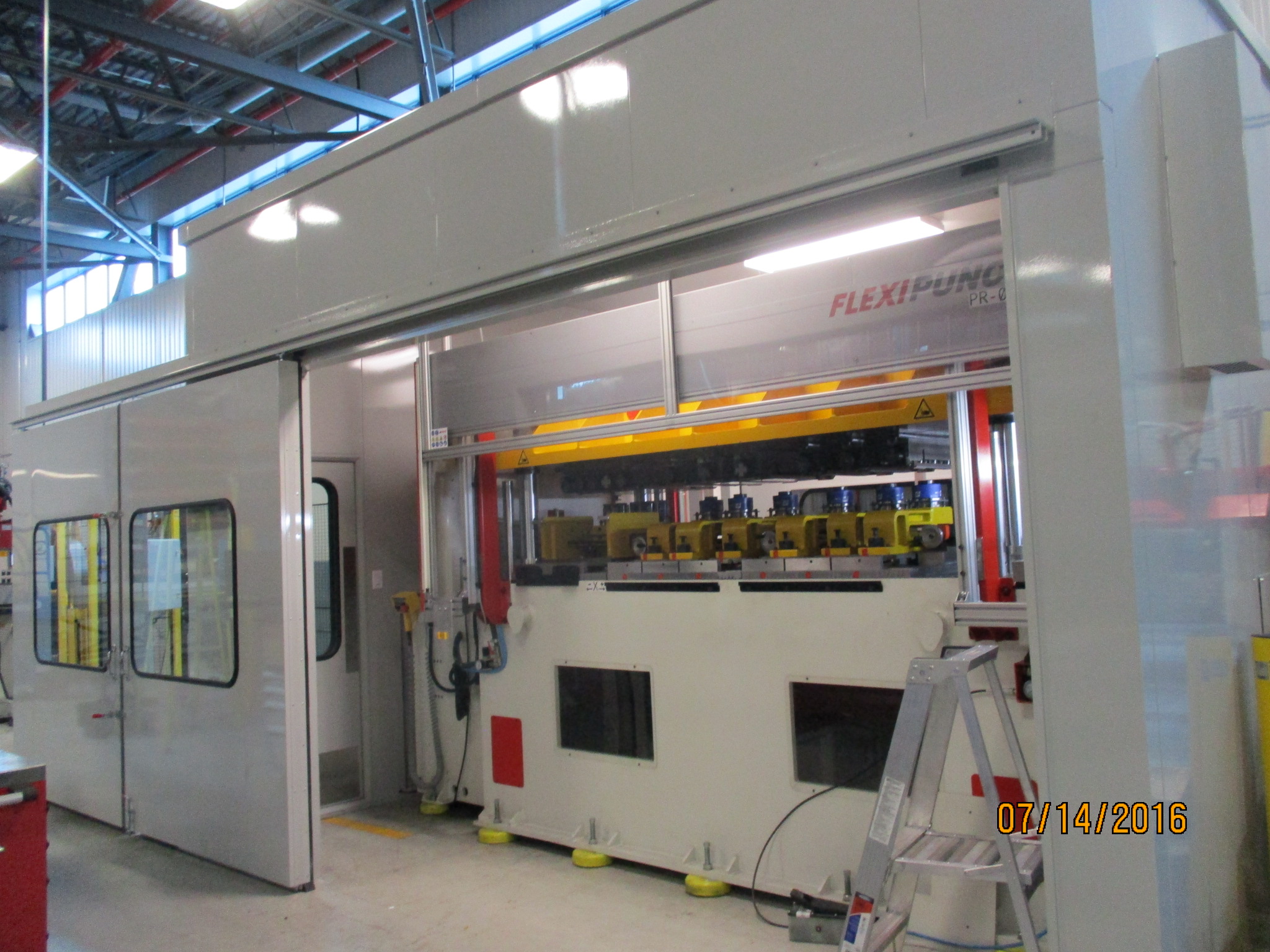
Acoustic Sound Enclosures for Machinery & Equipment
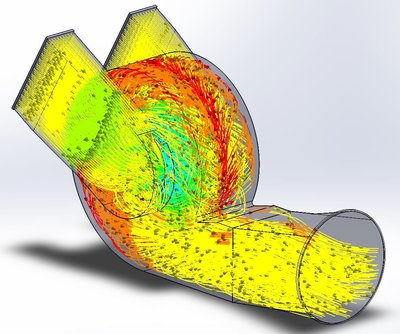
How to reduce industrial fan noise, hum or drone without attenuators with improved efficiency - Industrial Noise & Vibration Centre

Industrial Noise Enclosures for Industrial Noise Control
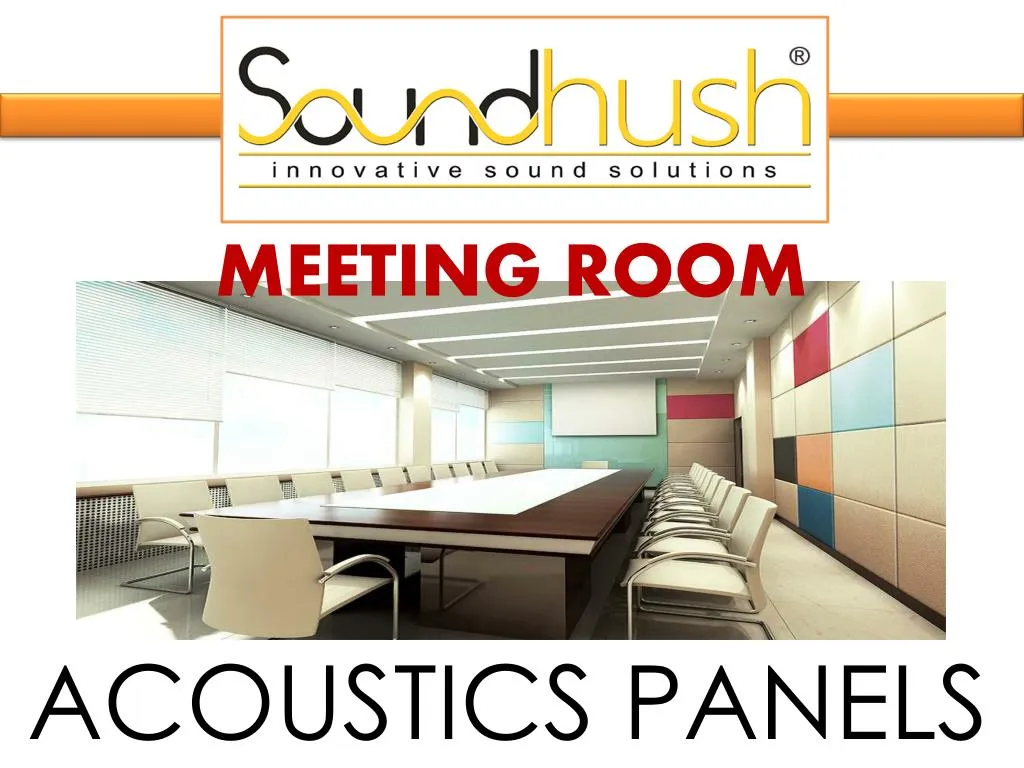
PPT - Sound Hush-meeting room acoustic panels PowerPoint Presentation, free download - ID:7565087

Industrial Acoustic Enclosures - Sound Seal
FanAir Company

Blowers and Compressors Acoustic Enclosures - Acoustic Enclosures for Blowers Manufacturer from Greater Noida
FanAir Company
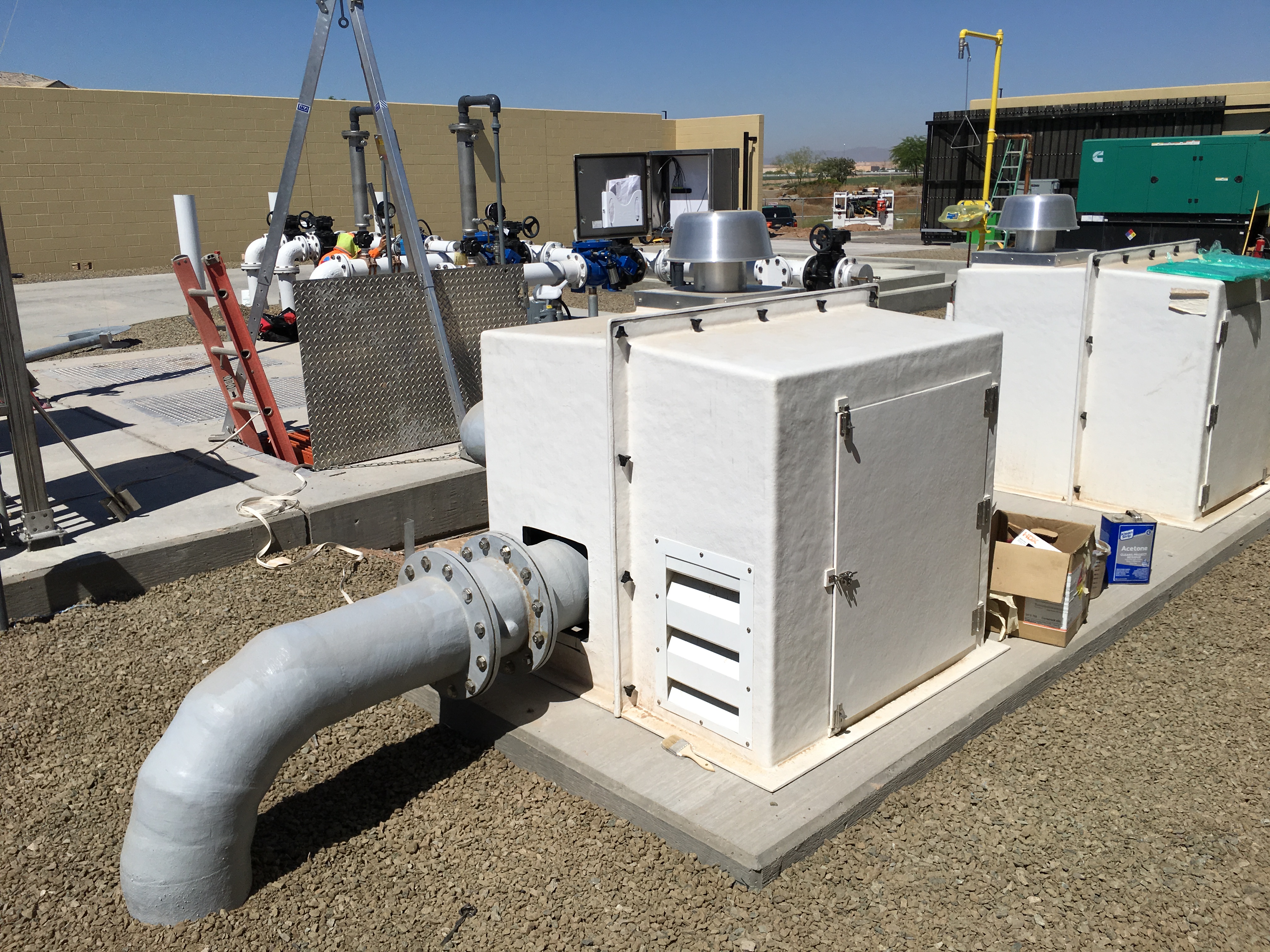
Acoustic Sound Enclosures for Blowers, Fans, Pumps and Compressors

Acoustic Enclosures for Industrial Equipment - IAC Acoustics

Industrial Acoustic Sound Enclosures FanAir Company designs and builds Acoustic Sound Enclosures Engineered to each specific application to control noise. - ppt download

Industrial Noise Enclosures

Acoustic Enclosure
de
por adulto (o preço varia de acordo com o tamanho do grupo)